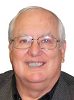
Gary Lownsdale combines vision with realism
(EDITOR’S NOTE: This is the second in a two-part series covering a recent presentation that Gary Lownsdale made during a recent Advanced Composites Cluster meeting in Oak Ridge.)
By Tom Ballard, Director of Innovation and Entrepreneurial Initiatives, Pershing Yoakley & Associates, P.C.
Gary Lownsdale is a visionary who is also a realist.
As noted in the first article in this series, he saw where the automotive industry was headed several years ahead of the bankruptcy of Chrysler and General Motors as well as many suppliers.
Today, the industry veteran is upbeat about the sector and extremely passionate about the role that emerging technologies are playing. At the same time, Lownsdale is also realistic about the challenges that face one of his favorites – carbon fiber composites.
The triple retiree shared his insights during a recent Advanced Composites Cluster meeting hosted by Roane State Community College and the East Tennessee Economic Council.
“We think hybridization is where the next revolution in materials is going to occur,” he said. “We’re looking at hybrid fibers, not just carbon fiber.”
This means using carbon fiber in conjunction with other, less expensive materials, to provide solutions that address the cost pressures the industry faces.
Carbon fiber is a very strong and extremely lightweight material that is only used in high-end products like cars and airplanes due to its cost. With new federal standards driving-up fuel efficiency standards, carbon fiber composites become an attractive alternative to maintain structural integrity while also reducing vehicle weight.
“Cost continues to be a driver,” Lownsdale said, adding that “the magic bullet (for carbon fiber) is $5 per pound.” This would cover both the cost of the raw material as well as all processing.
Price is not the only challenge to widespread use of carbon fiber. Other obstacles range from the dynamics of the global economy to the realities of how quickly a supply chain can be created.
Lownsdale noted that carbon fiber is a petroleum-based product that it is mostly produced overseas.
As if this dual dependence on other countries was not enough, he added that the current global supply of carbon fiber is insufficient to produce the estimated 10 pounds per vehicle needed to sufficiently reduce a car’s weight to meet the new U.S. fuel efficiency standards.
“Our needs far exceed world capacity,” he said, adding that it is not easy to increase output in the U.S. or other countries. A new carbon fiber production plant takes three to four years to build and an investment of $150 million or more.
The financial challenge for a company wanting to produce carbon fiber parts is equally daunting, reaching $25 million to set-up a plant to produce significant quantities.
“You’re seeing a slowdown in composites due to a lack of capital,” Lownsdale said.
Another challenge is a well-prepared workforce.
“Production workers need a different set of skills,” Lownsdale said, but quickly added, “Engineers do, too.”
In the case of the latter, the requirements include an understanding of manufacturing as well as product design and computer-aided engineering.
“This is a real challenge for the education community,” he said. “They can’t wait for the industry to pull them along. They have to anticipate the future.”
Lownsdale noted local leadership in technology development and workforce preparedness, praising Roane State for its training programs and Oak Ridge National Laboratory for its research to develop a biomass precursor for carbon fiber.
Like what you've read?
Forward to a friend!