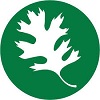
PART 2: MDF started with six focus areas, now emphasizing additive manufacturing and composites
(EDITOR’S NOTE: This is the second article in a multi-part series focused on the U.S. Department of Energy’s Manufacturing Demonstration Facility {MDF} at Oak Ridge National Laboratory {ORNL}, truly one of the Knoxville-Oak Ridge region’s greatest technology and innovation assets The first three articles examine the MDF from the perspective of ORNL; the other three spotlight ways that local companies are capitalizing on the facility.)
“We set it up in a way to focus on all six areas,” says Bill Peter, Director of the U.S. Department of Energy’s (DOE) Manufacturing Demonstration Facility (MDF) at Oak Ridge National Laboratory (ORNL). Those areas, as outlined in Part 1 in this series, were lightweight materials, additive manufacturing, composites, roll-to-roll processing, low temperature synthesis, and transient field processes.
“Within two years, we decided to reduce our focus to two areas – additive manufacturing and composites,” he explained. After all, the MDF was a start-up, and new ventures are best served when they limit their focus in the early years.
“In addition to bringing in research dollars, we also launched a technology collaborations program,” Peter said. That initiative, named the “MDF Technical Collaborations Program” (TCP), was described in this March 2013 teknovation.biz article as “a ‘seedling program’ to develop a proof of concept” . . . “a short-term collaborative technology assessment intended to accelerate commercial implementation of advanced manufacturing and materials technologies.”
Peter elaborated, saying it was “a fast track, non-negotiable CRADA,” referencing the Cooperative Research and Development Agreement that takes time to negotiate because of items like intellectual property ownership. “The (TCP) terms were very favorable for industry. The contract could usually get reviewed within 30 days.”
That tool made a statement to manufacturers that ORNL really wanted to build collaborative partnerships.
When the MDF opened, Peter says the Advanced Manufacturing Program was hosting about 1,000 visitors annually. Today, it averages about 5,000 people per year from 700 to 1,000 different companies. Visits are important, but what comes out of them is a higher priority.
“We start about 30 new projects annually with industry,” Peter says. “The MDF has one-half of all of the collaborative research projects undertaken at ORNL.”
Problem solving and new opportunities are clearly the emphasis at the MDF, enhanced by an interdisciplinary approach that involves researchers from multiple ORNL disciplines working alongside researchers from the companies.
“That has created a ‘can do’ attitude,” Peter explains. “Our success is based on the company’s success.”
In addition to what you might think would be the normal benefits to ORNL and its scientists, there’s one that might surprise you until readers give it more thought.
“You hear the heartbeat of America,” Peter says, citing what he calls the “raw information” that is shared during those collaborations. “You’re almost like a shrink for industry,” and those insights further inform the ORNL research agenda for the future.
We asked for an example.
“Take tooling and our dependence on technology from overseas,” Peter said. Those who are in manufacturing clearly understand the magnitude of this challenge. So, the MDF is helping companies understand how they can utilize rapid prototyping and advanced manufacturing of tooling that can be used in a large range of applications including composites, stamping and injection molding allowing companies to innovate much faster.
As a result of the significant growth in the number of companies visiting the lab and the annual volume of projects, Peter says the big equipment manufacturers want to place their equipment in the MDF at no cost as part of the R&D. That allows them to draw on the experience and knowledge of ORNL scientists while also allowing companies to test these new machines before making what most likely are significant financial investments.
“We fill-in knowledge gaps,” Peter says.
Now, with the MDF housed in a larger building, ORNL has more space for more collaborations with industry. The space is largely allocated to one of six focus areas – composites and polymer systems, large scale metal systems, machine tooling, manufacturing analytics and simulation, metal powder systems, and metrology and characterization – in addition to offices and conference rooms.
NEXT: Some new people and some exciting new areas of focus.