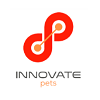
PART 1: Innovate Pets looked in five counties for just the right building
(EDITOR’S NOTE: This is the first article in a two-part series describing one of the area’s newest manufacturers that is part of an effort to bring manufacturing back to the U.S. To do so, the team behind Innovate Pets had to scour East Tennessee to find a suitable building. Part 1 describes that process.)
By Tom Ballard, Chief Alliance Officer, PYA
Remember the old saying, “What you see is what you get”? That phrase clearly applies in several ways to the new plant that Innovate Pets just opened in Loudon’s Blair Bend Industrial Park.
“We turned over a lot of rocks in five counties before we found this vacant building,” Scott Huff of the Innovate family of companies told us during a recent tour of the building that formerly housed a steel distribution company. Also joining us on the tour – our first since the space was finalized – were Chatchai Lertviwatkul, General Manager, and Mike Griffin, Operations Manager.
Innovate Manufacturing, described in this recent teknovation.biz article, is located in the Hardin Valley area of West Knoxville. Like its sibling, Innovate Pets is another effort by Huff to bring more manufacturing jobs back to the U.S.
“The process for this product (a consumable pet tooth brush) is very driven by the facility layout,” Huff said. “There’s not much consumable molding in the U.S. Finding a building to fill a niche like this was challenging.”
In essence, Huff had to identify a building and visualize what the shell would look like after he installed all of the equipment that would be used.
The selection criteria included a plant that had a long footprint, overhead cranes to handle tooling, and a floor that would support the very heavy equipment. The building Huff finally found in London met those criteria, but it was only a shell.
“Our investment, which was significant, was in the buildout,” he explained. That process included a cleanroom where the raw material, specifically a lactose and fat free milk protein called casein, is mixed before being fed to the molds that actually make the product. There was also a significant power requirement.
“That was very challenging,” Huff said. “Electricity on the scale we needed was not here. We had to be able to scale over time . . . three levels of electric.”
The building did not have loading docks. Under its previous use as a steel distribution facility, the building’s owner had the trucks on which the steel was loaded simply drive onto the reinforced floor through a door on one side of the building and exit on the other side. The loading docks had to be built in an area that was also expensive because of the challenge incurred in stabilizing the ground.
“We’re not done with infrastructure,” Huff said. The next big spend is to add more electricity for additional heating, ventilation and air conditioning.
Over the next three to five years, Innovate Pets will add additional manufacturing lines and additional equipment to further automate processes like final packaging before shipment. One thing that will not change is the overall size of the facility. That’s not because Huff does not want to grow, but rather a limitation caused by the lack of expansion space in the current location.
NEXT: The product and the process.
Like what you've read?
Forward to a friend!