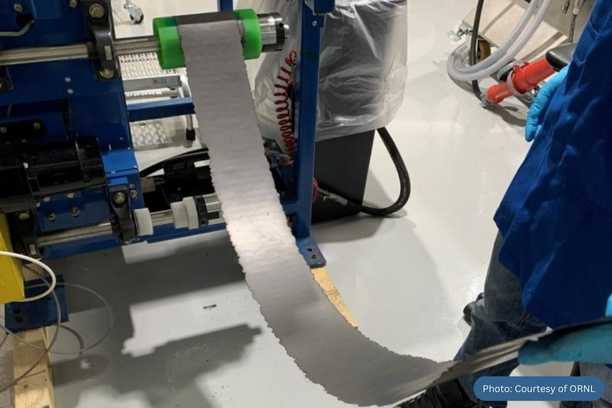
ORNL researchers explore dry manufacturing process for lithium-ion batteries
The relatively new alternative saves factory floor space as well as time, energy, waste disposal and start-up expenses.
The lithium-ion batteries used to power electric vehicles are key to a clean energy economy. But their electrodes are usually made using a wet slurry with toxic solvents, an expensive manufacturing approach that poses health and environmental risks.
Early experiments by scientists at Oak Ridge National Laboratory (ORNL) have revealed significant benefits to a dry battery manufacturing process. This eliminates the solvent while showing promise for delivering a battery that is durable, less weighed down by inactive elements and able to maintain high energy storage capacity after use. Such improvements could boost wider EV adoption, helping to reduce carbon emissions and achieve U.S. climate goals.
Dry processing is a relatively new alternative that saves factory floor space as well as time, energy, waste disposal and start-up expenses, yet until now, researchers have had limited understanding of how and why it works.
ORNL researchers and industry partner Navitas Systems probed how the dry process affects the structure of battery materials and their electrochemical properties. Batteries generate energy as lithium ions travel between electrodes called the cathode and anode. The team focused on an electrode dry processing strategy, which involves mixing dry powders with a binder, then compacting the material to improve contact between the particles. This strategy could be applied to both the anode and cathode by focusing on either certain materials or mixing methods.
The results of the collaboration have been published in the Chemical Engineering Journal. Click here to learn more.
Like what you've read?
Forward to a friend!