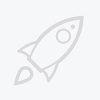
Ming Qi’s commitment is driving local start-up Peroxygen Systems
By Tom Ballard, Chief Alliance Officer, PYA
“Being an international student and doing a start-up is not easy,” Ming Qi says, but he quickly adds, “Wanting to have this type of career gave me the courage.”
Today, the 2013 graduate of the University of Tennessee (UT) with a Ph.D. in Chemical Engineering is the Co-Founder and Chief Technology Officer of Peroxygen Systems, Inc. The company is focused on commercializing a break-through technology for producing hydrogen peroxide onsite, targeting the paper and pulp industry.
Qi is joined in the endeavor by Tom Zawodzinski, one of the holders of the prestigious Governor’s Chairs at UT and Oak Ridge National Laboratory. The two are the inventors pf the patents for the technology that is the foundation of the company.
“It’s pretty cool and exciting,” the Chinese-born scientist turned entrepreneur says.
Qi won this year’s Tennessee Venture Challenge and $20,000 to advance the start-up’s efforts. The event was sponsored by the UT Research Foundation as one of the ways it helps accelerate the commercialization of UT inventions.
A conversation with Qi quickly convinces you that he has a genuine passion for the technology and the impact it will have on the industry Peroxygen Systems is targeting as well as the environment.
“The paper and pulp industry is a perfect fit for us,” Qi says. “The industry needs a less expensive bleaching agent and using our technology will not only cut their cost, but also help them operate greener at the same time.”
According to Wikipedia, bleaching of wood pulp is the chemical processing carried out on various types of wood pulp to decrease the color of the pulp, so that it becomes whiter. The main use of wood pulp is to make paper where is an important characteristic.”
Qi explains that chlorine, which is a toxic and environmentally-unfriendly chemical, is frequently used in the bleaching process. A better alternative is hydrogen peroxide (H2O2) as evidenced by the fact that about 45 percent of the amount produced each year globally is used for paper and pulp bleaching.
There are challenges, however, in the use of H2O2. The hydrogen peroxide is usually produced at a central location, then transported to the site of the end user where it must be off-loaded and stored before being diluted ahead of its actual use in the bleaching process. This multi-step process adds costs and elevates the safety risks at each step.
Peroxygen Systems approach is to build a hydrogen peroxide production unit on the site of the pulp or paper mill. The start-up believes it will save the customer money in the end.
“It is a much more efficient process,” Qi explains, noting an additional benefit is the elimination of pollution.
The company has pilot-tested a medium-size prototype that produced a 50 percent savings over the traditional option currently available. Now, the focus is on scaling-up to a larger size prototype module. That should be completed by the end of 2016.
Peroxygen Systems has different pulp mills that are interested in using its technology.
“We have a very good understanding of how we can install our equipment in their plant,” Qi says. “We just have to prove ourselves and earn their trust.”
Like what you've read?
Forward to a friend!