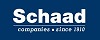
Jenny Banner remains focused on a “revolution” in home design and construction
She’s four years into a revolutionary project to change the way that homes are designed, built and equipped, and she’s as optimistic about the endeavor today as she was when I first discussed it with her in 2008.
The “she” is Jennifer Banner, Chief Executive Officer (CEO) of Schaad Companies, a 102 year-old family-owned company focused on commercial and residential construction, development, brokerage, management, and investments.
The “revolutionary project” is the ZEBRAlliance, a public-private partnership that Schaad Companies spearheaded to convince homeowners that energy-efficient houses can be real, desirable and affordable. Other key partners include Oak Ridge National Laboratory (ORNL), BarberMcMurry Architects, U. S. Department of Energy (DOE), and Tennessee Valley Authority (TVA).
“We were pioneers when we started this, and we still are,” Banner told teknovation.biz in a recent interview.
For the researchers at ORNL, it was fortunate that Banner and her colleagues at Schaad Companies were willing to start the journey on the cusp of the housing crisis and economic downturn. I know firsthand, because I had been in the mix to find a partner to help ORNL move from building single, one-of-a-kind homes with Habitat for Humanity to a larger scale platform with multiple houses constructed at the same time.
The ORNL team at the time also included Dana Christensen, then Associate Laboratory Director for Energy and Engineering Sciences; Patrick Hughes, then the Building Technologies Integration Manager; and Jeff Christian, a researcher who had spearheaded the construction of four “near zero energy homes” in Lenoir City. Both Christensen and Christian have left ORNL.
When the discussions with Schaad Companies started, ORNL had commitments from the U.S Department of Energy (DOE) to fund additional research focused on building methods and appliances, but it had to find partners. Some had been secured in areas like heating, ventilation and air conditioning (HVAC), water heaters and kitchen appliances. What was missing was a company that would not only build several houses, but incur the cost of keeping them off the market for several years while research was underway.
ORNL found its construction partner in Schaad Companies where Banner, a Certified Public Accountant turned CEO, had a passion for energy efficiency and a desire to enhance the company’s brand. It helped that she was also willing to devote the time to fully understand the science behind the project.
Banner uses today’s modern automotive assembly process to draw both similarities and differences with home construction. In the case of an automotive plant, she notes that “the company controls assembly for things like door fits.” The automotive manufacturer develops the specifications, and the supplier is expected to produce parts or components just-in-time and to very exacting standards.
While standardization is important in manufactured housing, that’s not the case with “stick-built” homes which were the target of ORNL’s research and the Schaad Companies’ interest.
“Traditional home construction is decentralized,” Banner explains. “It uses a host of subcontractors . . . framers, plumbers, roofers, sheet rockers to name a few. Compared to a manufacturing plant full of robotics, home construction drives scientists crazy (because) it’s fraught with the human element and human beings are capable of human errors.”
“We said we would take these challenges and address them,” she said.
One of the early challenges for Banner was fully understanding the nuances between the Energy Star and Builders Challenge building programs and deciding which of the two programs to use as the guide for the ZEBRAlliance homes.
Energy Star, now in its third iteration, is a joint initiative of DOE and the U. S. Environmental Protection Agency to help consumers save money and protect the environment through energy-efficient products and practices. It is most known to the public for the ratings on refrigerators, washers and dryers, computers, and other appliances. Lesser known to the public is the fact that Energy Star is a designation whole homes can attain.
The Builders Challenge, another DOE building program, arguably is a more rigorous standard for home construction than Energy Star, including not only energy efficiency requirements, but also construction quality requirements. However, the marketplace has been slow to acknowledge Builders Challenge.
Banner explained that it has taken more than a decade “to get the nation to recognize the Energy Star mark.” After studying the differences between Energy Star and Builders Challenge, Banner has concluded that the Builders Challenge “is a more rigorous designation to attain and is probably superior to Energy Star, but it lacks brand recognition.” She believes that long-term success for the ZEBRAlliance project requires having a universally-recognized certification for energy efficient homes.
The Schaad-ORNL team has certified the ZEBRAlliance homes to meet Builders Challenge standards, but Banner says that the marketplace recognizes Energy Star, which the homes also meet (and exceed). For this reason, marketing of the ZEBRAlliance homes, at the end of the scientific study, may focus on the Energy Star designation.
With that decision behind her, Banner turned to another key challenge: answering the question, “How do you improve the manufacture of something that has historically been so decentralized and so human?”
NEXT: The ZEBRAlliance tackles the challenges.
Like what you've read?
Forward to a friend!