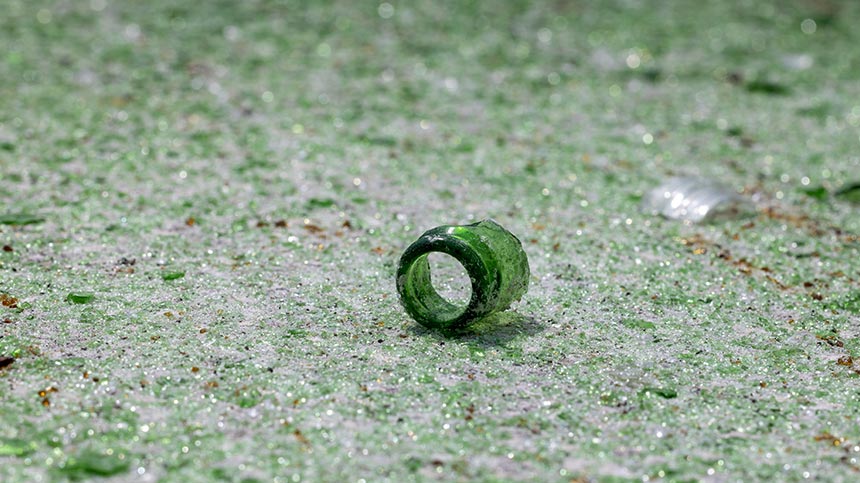
IC COHORT 6 | Vitriform3D Inc. creating product opportunities using recycled materials
Meet the founders of Vitriform3D, part of Cohort 6 of Oak Ridge National Lab's Innovation Crossroads program.
The two Co-Founders of Vitriform3D Inc. met while they were working on their doctorates as part of the Bredesen Center for Interdisciplinary Research and Graduate Education at the University of Tennessee, Knoxville (UTK).
After initially collaborating together as they pursued their degrees, they have now launched a start-up with the goal of creating product opportunities that use recycled materials like glass rather than sending them to a landfill. It’s a big challenge considering the current economics but one about which Dustin Gilmer and Alex Stiles are very passionate and which the latter will be pursuing over the next two years as part of Cohort 6 of the “Innovation Crossroads” (IC) program operated by Oak Ridge National Laboratory (ORNL).
Gilmer grew up in nearby Kingsport, while Stiles was raised in Kenosha, WI. They met when Gilmer, who was working at Oak Ridge National Laboratory’s Manufacturing Demonstration Facility as part of his doctoral activities, needed help doing some tests related to binder jetting. It is an additive manufacturing process in which an industrial printhead selectively deposits a liquid binding agent onto a thin layer of powder particles – foundry sand, ceramics, metal, or composites.
Gilmer (pictured left) found the testing expertise in Stiles who had been involved in a number of collaborative composites-related projects with Uday Vaidya, the well-known expert who holds multiple positions as a UT/Oak Ridge National Laboratory (ORNL) Governor’s Chair in Advanced Composites Manufacturing; UTK Professor of Mechanical, Aerospace and Biomedical Engineering; and Chief Technology Officer for the Institute for Advanced Composites and Manufacturing Innovation (IACMI).
“We began bouncing ideas off each other,” Stiles (pictured above) told us. One of their top concepts was to use binder jetting with glass material to create new products rather than simply sending what amounts to eight million tons of glass annually into a landfill.
“If you take glass and shatter it, the resulting material becomes very similar to sand,” Gilmer explains. Today, Vitriform3D is using a patent-pending binder jet technology to enable large-scale 3D printing of a wide range of recycled powders, starting with pulverized glass. The start-up, which launched a little more than a year ago, has a license option for the technology through the UT Research Foundation.
It’s not Stiles’ first start-up. As an undergraduate student at Illinois Institute of Technology, he launched a bamboo fiber composites company called Samambu LLC and won awards at three business plan competitions
Part of the challenge the two are addressing at Vitriform3D is the economics. It starts with the fact that only about a third of the glass waste produced each year is recycled. To make it economical, a processing facility capable of recycling the glass must be within 150 miles of the collection point. That was one of the factors that led the City of Knoxville to stop accepting glass in residential recycling several years ago, Gilmer and Stiles said.
“The challenge is not getting the glass,” Stiles explains. “It is finding those end users for products that can be made from the material.”
The Co-Founders see early opportunities to use pulverized glass to make value-added polymeric composite products in areas like tooling, dies, molds, and fixtures. Those require what Stiles describes as isotropic capabilities to expand and contract in a predictable way.
For Gilmer, Vitriform3D is his after-hours activity while he is a full-time Post Doc working with UTK’s Tony Schmitz, a Professor of Mechanical Engineering and the guru behind America’s Cutting Edge (ACE), an initiative designed to help close the skills gap and restore American dominance in machine tool technology and innovation. Stiles, on the other hand, is devoting full-time to the start-up. He outlined the goals for the two-year IC effort as follows:
- Get the prototype printer that will use glass and other inorganic waste materials as recycled feedstocks totally finalized;
- Demonstrate the technology in a proof of concept; and
- Secure follow-on funding for a larger scale, closer to commercially-ready printer.
“We’re very focused on glass but will be looking at other materials,” Gilmer says. “Glass is our best starting point.”
Like what you've read?
Forward to a friend!